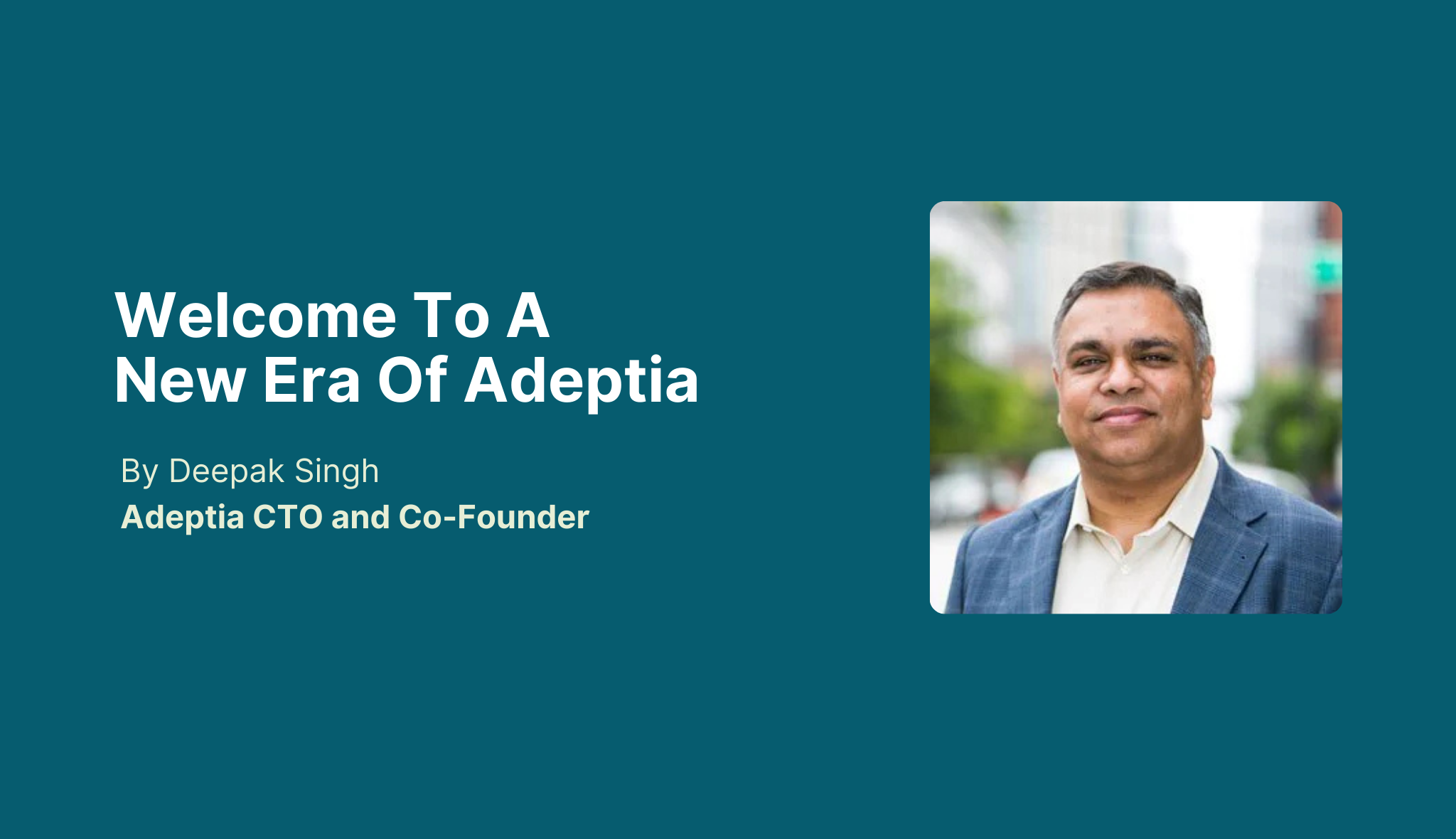
Welcome to a New Era of Adeptia Connect
Today, Adeptia launched the latest version of Adeptia Connect, which includes several exciting new enhancements! Hear from CTO and cofounder Deepak Singh what this means for our customers and prospects.
A global leader in labeling and packaging materials used Adeptia's automated order capture solution to reduce order processing from days to minutes, eliminate manual data entry errors, and scale operations by automating 80% of processes, allowing staff to focus on higher-priority tasks.
Company Size
Enterprise
Industry
Small Label Manufacturing
Customer Stories
Small labels are big business, especially when speaking about a global leader in labeling and packaging materials and solutions. Unfortunately, operations were neither smooth nor seamless when it came to receiving and processing orders for garment labels, a major department within the manufacturing firm. With hundreds of customers submitting orders in approximately 50,000 different formats, the company was facing an order processing nightmare. In response to the data difficulties, the manufacturer explored the possibility of asking customers to provide orders in a specific format. However, that would place the burden of responsibility on the customers’ side. Instead, the company implemented an internal and manual solution — hire thousands of customer service representatives. These representatives took orders as they were received, checked the information, and contacted customers to fill any gaps. Afterwards, they put the data into a standard file structure and forwarded it to a separate order entry team. The entry team then entered the data into the backend systems. The system was cumbersome, inefficient, and resource-intensive. To support the manufacturer’s continued growth in the market and remain competitive, an automated solution was needed.
After evaluating several tools, the company chose Adeptia’s automated order capture solution. Adeptia enables the company to receive orders from any source (including APIs, XML, web services, cloud applications, portals, etc.) and in any format (for instance, Electronic Data Interchange (EDI) transactions, Excel spreadsheets, PDFs, Word documents, email attachments, etc.). The system dynamically reviews the order data according to defined rules and alerts a customer service representative if additional information is required. Once an order is complete and validated, it is automatically translated and mapped into the backend ERP system for processing.
Thanks to Adeptia, the company was able to: